- Get link
- X
- Other Apps
%20(1).avif)
Forklift safety is paramount in maintaining a secure and efficient workplace, particularly in industries reliant on heavy machinery. In the UK, adhering to updated forklift safety rules is not just a legal obligation but a critical aspect of protecting workers and pedestrians on-site.
This blog aims to inform and guide you on the top five essential forklift safety rules you need to know. By understanding these guidelines, you can enhance forklift pedestrian safety, ensure compliance with safety regulations, and promote a culture of vigilance and responsibility in your workplace. These fundamental rules help you create a safer and more productive environment for the business and its workforce.
The 5 essential safety rules we’re focusing on today include:
- Comprehensive Training and Certification
- Regular Equipment Inspections and Maintenance
- Safe Operating Practices
- Proper Use of Safety Gear and Equipment
- Implementing Safety Signage and Procedures
Comprehensive Training and Certification
Ensuring that forklift operators receive proper training is crucial for maintaining a safe workplace. Trained operators are less likely to cause accidents, which can lead to serious injuries or even fatalities. Comprehensive training equips operators with the skills and knowledge needed to handle forklifts efficiently and safely, reducing the risk of mishaps and enhancing overall productivity.
Overview of Certification Requirements in the UK
The Health and Safety Executive (HSE) mandates that employers provide adequate training to all forklift operators. This includes basic training, specific job training, and familiarisation with the work environment. Certification is typically issued upon successful completion of a recognized training course, which ensures that operators meet the necessary safety and operational standards.
Updates to Training Protocols in 2024
As of 2024, updated training protocols have been introduced to further enhance forklift safety in the UK. These updates include more rigorous training modules, increased focus on practical skills, and the integration of advanced safety technologies.
These revised protocols aim to address the evolving challenges in forklift operations and ensure that operators are well-prepared to handle modern machinery safely and efficiently.
Benefits of Ongoing Training and Refresher Courses
Ongoing training and refresher courses are vital for maintaining high safety standards. Regular training sessions help operators stay up-to-date with the latest safety practices and technological advancements. Refresher courses reinforce essential skills and knowledge, preventing complacency and ensuring that operators continue to perform their duties safely. Continuous education fosters a culture of safety, reducing the likelihood of accidents and improving overall workplace safety.
If you want to learn more about forklift operator safety programs, here’s a guide for you.
Regular Equipment Inspections and Maintenance
Daily pre-operation checks are essential for ensuring the safe and efficient functioning of forklifts. Before starting any operation, operators should inspect their forklifts to identify potential issues that could compromise safety. These checks help in detecting problems early, preventing breakdowns, accidents, and costly repairs. By addressing issues before they escalate, daily inspections contribute significantly to maintaining a safe work environment.
Detailed Checklist for Forklift Inspections
A comprehensive inspection checklist ensures that no aspect of the forklift's condition is overlooked. Here is a detailed checklist that operators should follow during daily pre-operation checks:
- Visual Inspection:
- Check for any visible damage or leaks.
- Ensure all decals and warning labels are in place and readable.
- Verify the condition of the tires, looking for proper inflation and any signs of wear or damage.
- Fluid Levels:
- Check engine oil, hydraulic fluid, and coolant levels.
- Ensure there are no leaks or contamination.
- Operational Checks:
- Test the brakes, including the parking brake, to ensure they function correctly.
- Check the steering for smooth and responsive operation.
- Verify that all lights (headlights, taillights, warning lights) and indicators are working.
- Ensure that the horn and backup alarm are functional.
- Forks and Mast:
- Inspect the forks for cracks, bends, or excessive wear.
- Check the mast for smooth operation and ensure there are no obstructions or damage.
- Safety Devices:
- Confirm that seat belts, mirrors, and other safety devices are in good condition and properly adjusted.
- Check the load backrest extension for damage or misalignment.
Maintenance Schedule and Documentation
A regular maintenance schedule is crucial for keeping forklifts in optimal condition and ensuring long-term safety and efficiency. Establish a maintenance routine based on the manufacturer's recommendations and the forklift's usage. Typically, this includes:
- Daily Checks: Conduct the detailed preoperative inspections as outlined above.
- Weekly Maintenance: Inspect and clean air filters, check battery water levels, and ensure all bolts and fasteners are tight.
- Monthly Checks: Perform more in-depth inspections of the hydraulic system, tires, and overall forklift structure. Lubricate all moving parts as needed.
- Quarterly and Annual Maintenance: Conduct thorough inspections and servicing, including engine tune-ups, replacing worn-out parts, and comprehensive safety checks.
Documentation of all inspections and maintenance activities is vital. This documentation ensures accountability, helps track the forklift's condition over time, and provides valuable information for future maintenance planning.
Safe Operating Practices
Maintaining control over forklift speed is crucial for ensuring safety in the workplace. Operators should strictly adhere to speed limits set for various areas within the facility to minimise the risk of collisions and accidents. Additionally, following designated pathways helps in organising traffic flow, reducing the likelihood of accidents between forklifts and pedestrians. Clearly marked routes and proper signage further enhance safety by guiding operators and alerting pedestrians to forklift activity.
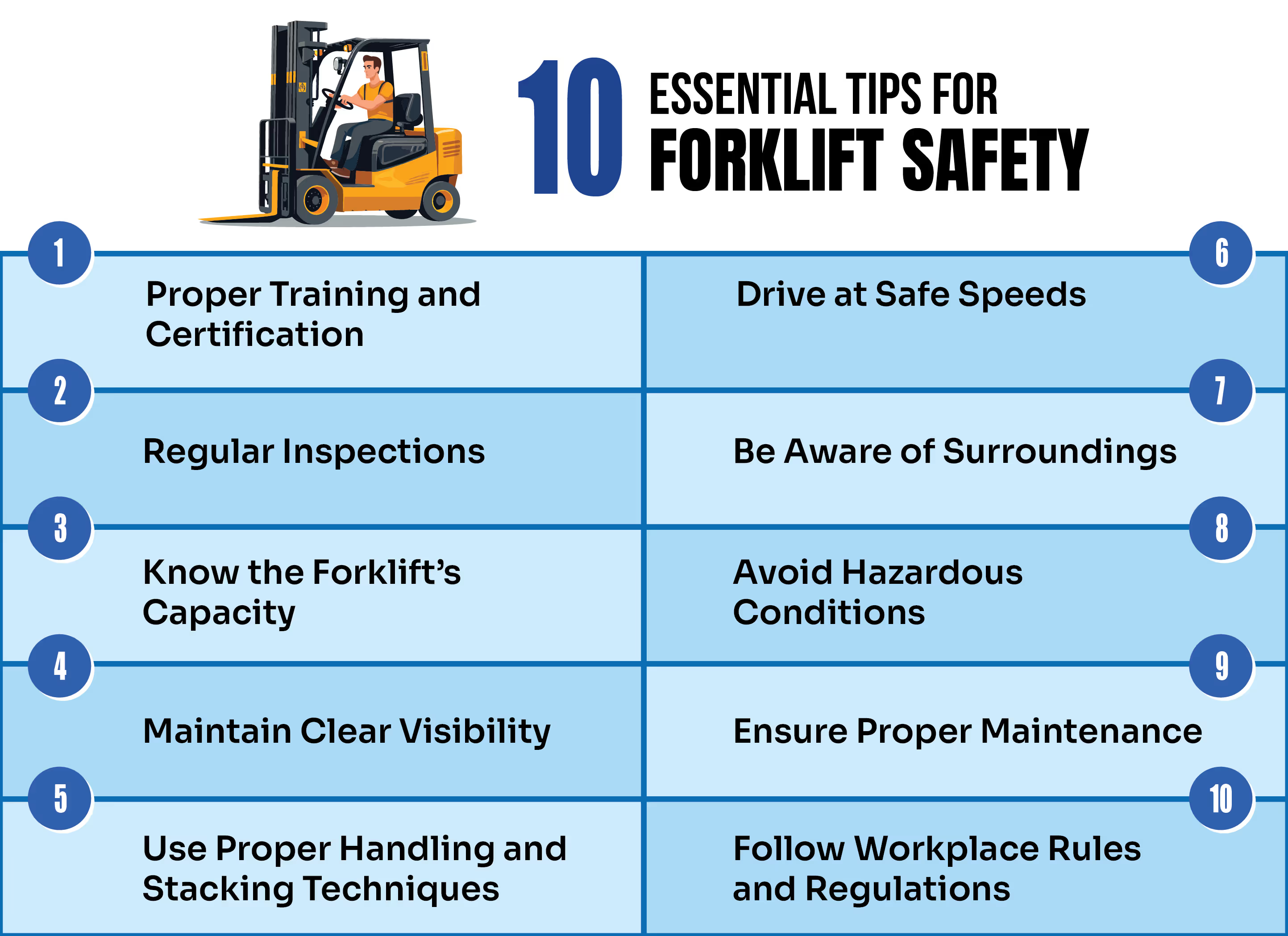
Guidelines for Handling Loads and Operating in Different Environments
Proper load handling is essential for preventing accidents and ensuring stability during forklift operations. Operators should:
- Always check the load for stability and secure it properly before moving.
- Ensure the load does not exceed the forklift’s capacity.
- Keep the load low to the ground and tilted back slightly while moving.
- Avoid abrupt movements and sharp turns, especially with a loaded forklift.
Different operating environments require specific considerations. For instance:
- In indoor settings, operators should be cautious of narrow aisles, low ceilings, and other obstructions.
- Outdoor operations demand attention to uneven surfaces, weather conditions, and potential obstacles like debris.
Adapting driving techniques to suit the environment helps in maintaining control and ensuring safety.
Importance of Visibility and Use of Lights and Signals
Visibility is a key factor in preventing accidents. Operators must ensure they have a clear line of sight and use the forklift’s lights and signals effectively:
- Use headlights when operating in dimly lit areas or outdoors during low visibility conditions.
- Engage warning lights and alarms to alert nearby workers and pedestrians.
- Utilise mirrors to enhance visibility, particularly when reversing or navigating tight spaces.
- Communicate intentions using hand signals or the forklift’s horn to alert others of movement.
Ensuring good visibility and effective use of signals can significantly reduce the risk of accidents involving forklifts and pedestrians.
SharpEagle can help you boost visibility and enhance your signals with quality equipment!
Updated Regulations on Safe Operating Practices for 2024
The 2024 updates to forklift safety regulations in the UK emphasise enhanced operational practices to further mitigate risks. Key changes include:
- Stricter enforcement of speed limits within workplace environments.
- More detailed guidelines on safe load handling, including mandatory training on securing and transporting various types of loads.
- Increased emphasis on using advanced safety technologies, such as collision avoidance systems and enhanced lighting.
- Regular audits and inspections to ensure compliance with updated safety standards.
Adhering to these updated regulations is essential for maintaining a safe working environment and ensuring compliance with legal requirements.
Proper Use of Safety Gear and Equipment
Mandatory Safety Gear for Forklift Operators
Ensuring that forklift operators wear the appropriate safety gear is crucial for their protection. In the UK, the following safety gear is mandatory for forklift operators:
- Helmets: To protect against head injuries from falling objects or collisions.
- High-Visibility Clothing: To ensure operators are easily seen by pedestrians and other machinery operators, reducing the risk of accidents.
- Safety Shoes: To protect feet from heavy objects and to provide better grip on slippery surfaces.
- Gloves: To enhance grip and protect hands from injuries and exposure to harmful substances.
By equipping operators with the right gear, employers can significantly enhance their safety and reduce the likelihood of injury.
Importance of Seat Belts and Other Safety Features
Seat belts are a fundamental safety feature that must be used at all times while operating a forklift. They help keep the operator securely in the seat, preventing ejection in the event of a collision or sudden stop. Other essential safety features include:
- Rollover Protection Systems (ROPS): Designed to protect the operator in the event of a rollover.
- Backup Alarms: To alert nearby workers when the forklift is reversing.
- Mirrors and Cameras: To enhance visibility and reduce blind spots.
- Load Backrest Extensions: To prevent loads from falling backward onto the operator.
Ensuring these features are functional and used correctly is crucial for maintaining a safe operating environment.
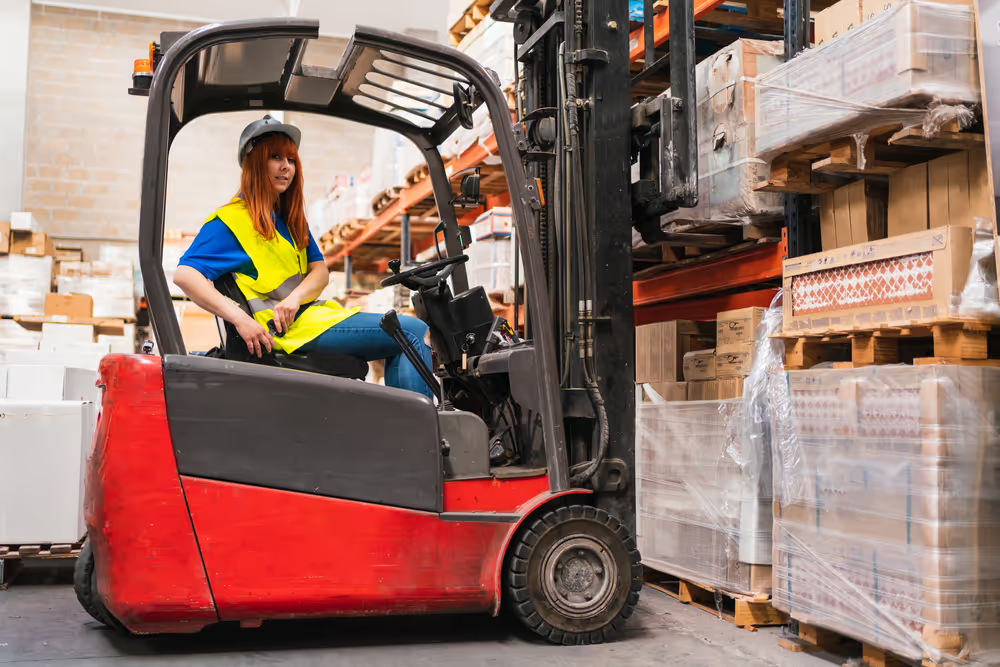
Encouraging a Culture of Safety Compliance Among Workers
Fostering a culture of safety compliance is essential for ensuring that all safety protocols are followed consistently. This can be achieved by:
- Regular Training and Awareness Programs: Educate workers on the importance of using safety gear and following safety procedures.
- Clear Communication of Safety Policies: Ensure all workers are aware of the safety policies and the consequences of non-compliance.
- Safety Audits and Inspections: Conduct regular audits and inspections to ensure compliance with safety standards.
- Encouraging Reporting of Safety Hazards: Create an environment where workers feel comfortable reporting safety concerns without fear of reprisal.
Implementing Safety Signage and Procedures
Clear and visible safety signage is vital in preventing accidents and ensuring a safe work environment. Safety signs communicate important information quickly and effectively, guiding operators and pedestrians in making safe decisions. Proper signage helps in identifying hazards, directing traffic, and providing instructions, thereby reducing the risk of accidents and promoting a culture of safety awareness.
Types of Signs and Their Meanings
Safety signs come in various types, each serving a specific purpose and conveying different messages. Understanding these signs and their meanings is essential for maintaining safety:
- Warning Signs: These signs alert workers to potential hazards or dangers, such as "Caution: Forklift Operating Area" or "Danger: High Voltage."
- Instructional Signs: Provide specific instructions or procedures that must be followed, such as "Wear Protective Gear" or "Keep Aisles Clear."
- Informational Signs: Offer general information or reminders, such as "Emergency Exit" or "First Aid Station."
- Prohibition Signs: Indicate actions that are not allowed, such as "No Entry" or "No Smoking."
Each type of sign uses specific colours and symbols to convey its message clearly and effectively. Explore our offer of safety signage here.
Updated Guidelines for Safety Signage Placement and Maintenance
As of 2024, new guidelines for the placement and maintenance of safety signage have been introduced to enhance workplace safety. Key points include:
- Placement: Signs should be positioned at eye level and in locations where they are easily visible to operators and pedestrians. They should be placed near potential hazards, entry and exit points, and along designated pathways.
- Consistency: Use standardised colours, symbols, and wording to ensure clarity and uniformity across the workplace.
- Maintenance: Regularly inspect signs for damage, wear, or fading, and replace them as needed to ensure they remain legible and effective. Ensure that signs are clean and unobstructed at all times.
Adhering to these updated guidelines helps maintain a safe and well-organised workplace.
Procedures for Emergency Situations and Reporting Accidents
Having clear procedures for emergency situations and reporting accidents is crucial for minimising harm and ensuring a swift response. Key procedures include:
- Emergency Situations:
- Establish clear evacuation routes and ensure they are marked with visible signage.
- Provide training on emergency response, including the use of fire extinguishers, first aid, and emergency shutdown procedures.
- Conduct regular emergency drills to ensure all employees are familiar with evacuation procedures.
- Reporting Accidents:
- Implement a straightforward process for reporting accidents and near-misses. Ensure all employees are aware of this process.
- Encourage prompt reporting of any incidents to ensure timely investigation and corrective actions.
- Maintain detailed records of all accidents and incidents, and analyse them to identify patterns and areas for improvement.
Conclusion
In this blog, we explored the five essential safety rules crucial for forklift operations in the UK. Adhering to these rules is vital for maintaining a safe and productive workplace, as each one plays a key role in minimising risks and protecting both operators and pedestrians.
As safety regulations continue to evolve to address new challenges and technological advancements, it’s essential to stay updated with any changes to these regulations to ensure ongoing compliance and uphold the highest safety standards. Regularly reviewing and updating safety practices in line with current regulations will help maintain a compliant and secure work environment.
To reinforce the importance of these safety rules, conduct regular training sessions, inspections, and safety audits. By prioritising safety and staying current with regulatory changes, you can foster a culture of vigilance and responsibility.
At SharpEagle Technology, we are dedicated to helping you achieve these goals. Our bespoke safety solutions are designed to ensure that your operations not only comply with the latest safety regulations but also enhance overall workplace safety. Let us be your partner in creating a secure and productive environment. Contact us today to understand how we can support your safety needs and ensure better compliance with the safety rules.
FAQs
1. What are the key components of forklift operator training in the UK?
Forklift operator training in the UK includes:
- Basic Training: Fundamental operations and handling techniques.
- Specific Job Training: Tasks related to the operator’s job and environment.
- Familiarisation Training: Getting used to particular equipment and workplace conditions.
- Certification: Passing assessments to ensure operators meet safety standards.
2. How often should forklifts undergo maintenance and inspections?
Forklifts should have:
- Daily Inspections: Pre-operation checks before each shift.
- Weekly Maintenance: Inspect air filters, and battery levels, and tighten fasteners.
- Monthly Inspections: Check the hydraulic system, tyres, and lubricate parts.
- Quarterly/Annual Maintenance: Comprehensive inspections and servicing, including engine tune-ups.
3. What are the updated safety signage guidelines for 2024?
Updated guidelines emphasise:
- Placement: Eye-level and visible locations near hazards and pathways.
- Consistency: Standardised colours, symbols, and wording.
- Maintenance: Regular inspections for damage, ensuring signs are clean and legible.
- Comprehensive Coverage: Clear marking of all hazards, instructions, and emergency procedures.
Comments
Post a Comment